The Variable reluctance machine (MRV) is an electric Simple construction, being one of the pioneers in the industry. The Industrial interest by MRV has been in place since 1850, with its Reduced use due to the complexity of triggering to the Technology of the time. With the advancement of Materials Engineering and Microelectronics, new drive techniques and control of Electrical devices have emerged, making it possible to use of electrical machinery that was once limited. The main Advantages of MRV are its simple construction, high robustness, Low cost of production and the expensibility of the use of materials Magnetic.
Besides The machine has fault tolerance that distinguishes it from other Electrical machinery, mainly due to the continuity of Operation in case of phase failure. The disadvantages are excessive Noise during operation, ripple in the electromagnetic conjugate Produced, Position information need (sensor coupled The rotor shaft) and high drive complexity of each phase.
The GPAR has a countertop consisting of a three-phase MRV, a Digital signal Controller (DSC) TMS320F28335, a sensor for Position, a three-phase asymmetric half-bridge converter and a Direct current machine connected to a load bank Resistive. The set is capable of triggering and controlling MRV, which can Also simulate the insertion of loads coupled to the shaft tip by Medium of the direct current machine.
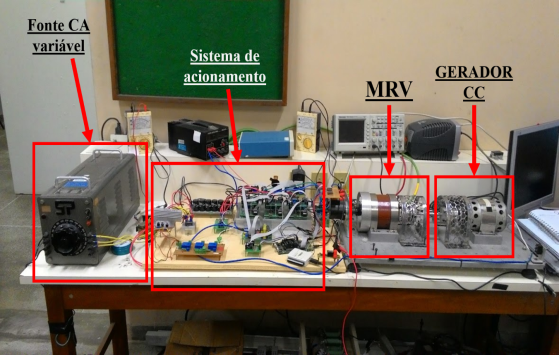